Ferrosilicon magnesium is mainly uses for producing cast ductile… In fact, this ferroalloy plays a significant role in providing magnesium for cast iron. Its basic chemical symbol is FeSiMg, it can change with changes in the atomic percentage of each element.
The best way for producing FeSiMg is Silicon thermal process
Iran FeSiMg
Iran Ferrosilicon magnesium is producing at different grades like below items:
- Si: 40% Mg: 5% Al: 1.2% Ce: 1% Size:1-5mm
- Si: 45% Mg: 6% Al: 1 % Ce: 1% Size:5-15mm
- Si: 50% Mg: 6.5% Al: 1% Ce: 1% Size:5-30mm
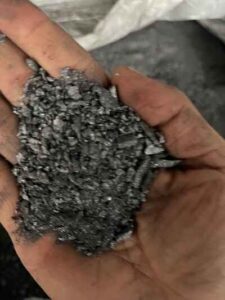
Iran Ferrosilicon Magnesium
Shape:
In comparison with Ferrosilicon, there is no distinctive different in shape and color and maybe you can’t recognize this both with each other.
Pricing:
Due to its superior specifications in compared with Ferrosilicon and also its various application at casting industries, it is more expensive than FeSi like double price. contact us for checking current price!
Ferrosilicon magnesium uses:
MgFeSi has various uses which you can find some of them as following items :
- Converting molecules of sheet graphites to spheres to produce all kinds of cast iron
- Increasing the strength and resistance of cast iron and also refinement of steel
- Production of all kinds of stainless steels in different grades
- Production of silicon steels
- Production of various carbon steels
- Making all kinds of unbreakable cast irons
- Binding agent
- Use in steel melting industry and various metals
Advantages of using ferrosilicon-magnesium in industry:
- It helps for increases germination in the melt so that you will get some higher quality in your casting.
- It increases the ferrite phase and reduces the brittleness of the parts
- It will be much easier for machinery your product when using MgFeSi in your casting.
- It reduces the use of carbides in casting thin sections
- Reduces operating costs as much as possible
The role of magnesium ferrosilicon in changing the microstructure of alloys:
In general, magnesium evaporates at temperatures above 1000 degrees Celsius. This element in its pure state has a strong affinity with oxygen. For this reason, they turn it into an alloy and use it to add magnesium to molten materials.
Ferrosilicon magnesium is usually added to the molds a little before the pouring operation. When the loading is done and the molten materials are freezing, magnesium is absorbed by the graphite buds and changes the surface tension of the graphite and causes the growth conditions to be uniform in all directions. Therefore, flake graphite become spheroids!
Adding ferrosilicon magnesium to cast iron alloys, in addition to making the graphite spherical, also increases the impact resistance, toughness and strength of the cast piece.
The method of preparation and production of magnesium ferrosilicon:
There are two methods for the production and preparation of ferrosilicon magnesium, and we will examine these two methods together.
- In the first method, the calcined ore of dolomite is regenerated by processes such as silicothermic or aluminosilicothermic, and the regenerating agents used in these methods include ferrosilicon or a mixture of ferrosilicon and aluminum.
Magnesium is produced in the reduction process, reacts with excess ferrosilicon and forms magnesium silicide (Mg2Si). This combination together with iron forms the ferrosilco-magnesium alloy material. The most important factors that affect this process are the amount of reducing agent and the type of flux added, i.e. limestone, fluorspar, bauxite and quartzite.
- In the second method, magnesium metal is immersed in molten ferrosilicon and ferrosilicon magnesium is produced.
Comparing the production costs of both methods indicates that the immersion method is more affordable. Today, the immersion of magnesium metal in molten ferrosilicon has been successfully tested on an industrial scale and has been very successful in the production of ferrosilicon alloy that has 5% magnesium